Celebrating 26 Years 1999-2025
Safeguarding Your Pressure-Relieved Systems with the REDEX® Flap
In the world of industrial processing, the safety and reliability of pressure-reduced systems are paramount. These critical components play a crucial role in maintaining the integrity of your operations, protecting both your equipment and personnel from the devastating effects of explosions. One of the key challenges in this domain is effectively isolating and containing the propagation of such explosions – a challenge that RICO Sicherheitstechnik AG has addressed with the development of the REDEX® Flap Valve.
The Importance of Explosion Isolation in Pressure Venting Systems
Pressure-relieved systems are widely used across a variety of industries, including food processing, chemical manufacturing, and pharmaceuticals. These systems are designed to release excess pressure in the event of an unexpected explosion or overpressure event, preventing catastrophic damage to the equipment and the surrounding environment. However, the very function that makes these systems so important also presents a unique challenge – the need to prevent the propagation of the explosion itself.
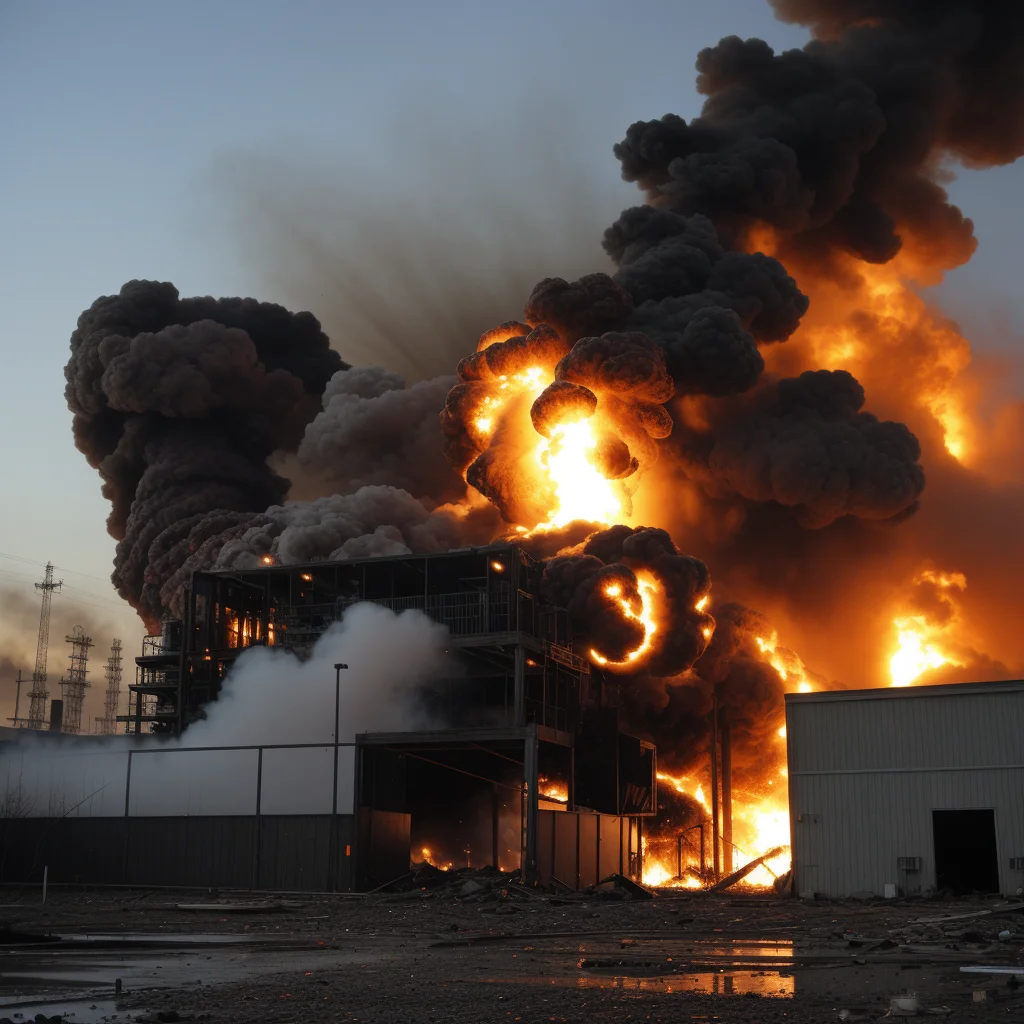
When an explosion occurs within a pressure-relieved system, the resulting pressure wave and flames can quickly spread, igniting additional combustible materials and leading to a cascading effect that can quickly spiral out of control. This phenomenon, known as explosion propagation, can have devastating consequences, jeopardising the safety of your personnel, the integrity of your equipment, and the overall continuity of your operations.
INTERESTED OR HAVE QUESTIONS? GET IN TOUCH WITH US NOW!
The REDEX® Flap: A Sophisticated Explosion Isolation Solution
Recognising the critical importance of effective explosion isolation, RICO Sicherheitstechnik AG has developed the REDEX® Flap – a durable and technically advanced explosion isolation flap valve that offers a comprehensive solution to this challenge.
Key Features and Advantages
The REDEX® Flap is designed with a focus on robustness and reliability, featuring a high-quality construction that ensures long-lasting performance. One of the standout features of this explosion isolation solution is its flexibility of use, thanks to its sophisticated certification and technology.
The REDEX® Flap’s passive functionality is another key advantage, as it does not require any additional detection or control mechanisms for its operation. This simplifies the installation and maintenance process, reducing the overall cost of ownership and making it a versatile choice for a wide range of pressure-relieved systems.
Maintenance costs are also kept low with the REDEX® Flap, as it can be serviced without the need for dismounting from the pipe. This quick and easy maintenance process saves time and effort, contributing to the overall efficiency of your operations.
Optimal system performance is another benefit of the REDEX® Flap, as its design ensures low pressure losses, allowing for efficient and unhindered flow of the medium during normal operation.
The REDEX® Flap’s mechanical locking system is a standout feature, providing the best possible protection against explosion propagation. This locking mechanism ensures that the flap disc is securely closed and locked in the event of an explosion, effectively preventing the spread of flames and pressure waves.
Finally, the REDEX® Flap offers the ability to monitor its function and potential dust deposits through the use of inductive switches. This feature allows for easy and reliable monitoring of the valve’s status, ensuring that any potential issues can be addressed promptly.
INTERESTED OR HAVE QUESTIONS? GET IN TOUCH WITH US NOW!
How the REDEX® Flap Works
The REDEX® Flap operates in three distinct modes to provide effective explosion protection:
Rest Position
In the rest position, with no air flow, the flap disc is in the closed but not locked position. In this state, the functional reliability of the REDEX® Flap is monitored by a dedicated switch.
Normal Operation
During normal operation, the flap disc is in the open position, allowing the medium to flow freely around it without obstruction.
Explosion Event
In the event of an explosion, the pressure wave pushes the flap disc into the closed and locked position. This action effectively prevents the propagation of flames and pressure waves, ensuring that the explosion is contained within the pressure-relieved system.
Approvals and Certifications
The REDEX® Flap has been extensively tested and certified to ensure its suitability for a wide range of industrial applications. The valve is approved for use with organic dusts up to a Kst value of 300 bar·m/s for the smaller models (DN140 to DN400) and 250 bar·m/s for the larger models (DN450 to DN710), making it suitable for a variety of process industries.
In addition to its ATEX certification, the REDEX® Flap is also approved for pull applications according to EN 16447:2014 (3.4). This standard covers the requirements for explosion isolation devices used in pressure-relieved systems, highlighting the REDEX® Flap’s suitability for these critical applications.
The REDEX® Flap is certified for use in Zone 20, 21, and 22 for inside and for use in Zone 21 and 22 for outside environment.
INTERESTED OR HAVE QUESTIONS? GET IN TOUCH WITH US NOW!
Installation Guidelines and Technical Specifications
The REDEX® Flap from RICO Sicherheitstechnik AG is available in a wide range of nominal sizes, from DN140 to DN710, allowing it to be tailored to the specific requirements of your pressure-relieved system.
Installation Considerations
When it comes to installing the REDEX® Flap, there are several important factors to consider. The valve must be positioned in a horizontal orientation, as this is the required installation position.
For the smaller REDEX® Flap models (DN140 to DN400), the applicable vessel volume range is between 1.0 m³ and 100.0 m³. The larger models (DN450 to DN710) can be used with vessels ranging from 0.7 m³ to 100 m³, or 2.77 m³ to 100 m³, depending on the specific nominal size.
It is essential to ensure that the REDEX® Flap is installed without any tension in the pipe and that it is supported separately from the pipe structure. This helps to maintain the proper functioning of the valve and prevents any potential issues caused by stress on the system.
Operating Conditions
The REDEX® Flap can operate within a wide temperature range, depending on the specific model. The smaller models (DN140 to DN400) can function between -20°C and +80°C, while the larger models (DN450 to DN710) have a range of +1°C to +100°C.
At temperatures below +1°C, it is crucial to ensure that the flap cannot freeze, as a frozen mechanism can negatively impact the proper functioning of the valve. This may require the implementation of additional measures, such as heating or insulation, to maintain the required operating conditions.
Pipe Configuration
The REDEX® Flap can be installed with a combination of pipe bends, with up to four pipe bends at the minimum installation distance. The pressure shock resistance of the pipeline on both sides of the valve must be designed in accordance with the safety concept used for the specific application.
If the REDEX® Flap is installed at an open pipe end, protective measures must be implemented on the side of the valve facing away from the explosion, in accordance with ISO 13857, to avoid the risk of injury.
Technical Specifications
The REDEX® Flap is available in a wide range of nominal sizes, each with its own set of technical specifications. Request a product documentation from CMC, that provides comprehensive information on the dimensional drawings, pressure drop values, and other technical details for each size below.
For the smaller models (DN140 to DN400), the maximum air speed against the explosion direction is 35 m/s, with a minimum closing pressure of the flap valve of at least 0.05 bar. The larger models (DN450 to DN710) have the same maximum air speed specification.
The pressure drop across the REDEX® Flap varies depending on the nominal size and the air speed, but the product is designed to maintain low pressure losses, ensuring optimal system operation.
INTERESTED OR HAVE QUESTIONS? GET IN TOUCH WITH US NOW!
Optimal Protection for Pressure-Relieved Filters
One of the key applications for the REDEX® Flap is as a raw gas side decoupling element in combination with pressure-relieved filters. These types of filters are commonly used in industrial processes to remove particulate matter from the airflow, and they often require effective explosion protection to ensure the safety of the overall system.
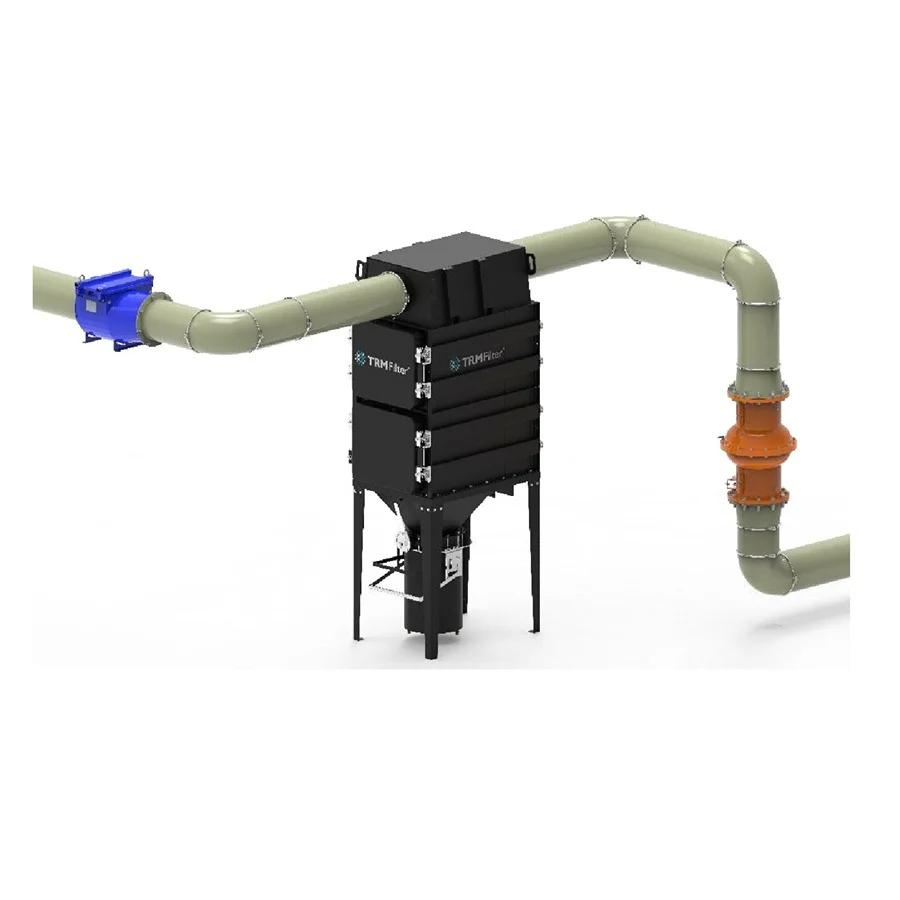
By installing the REDEX® Flap on the raw gas side of the filter, the propagation of flames and pressure waves can be effectively prevented in the event of an explosion. This provides a critical layer of protection for the filter and the surrounding equipment, helping to maintain the integrity and reliability of the entire pressure-relieved system.
Conclusion
In the dynamic and demanding world of industrial processing, the REDEX® Flap from RICO Sicherheitstechnik AG stands as a reliable and sophisticated solution for safeguarding pressure-relieved systems against the propagation of explosions. With its robust construction, passive functionality, and wide range of technical specifications, the REDEX® Flap offers a comprehensive approach to explosion isolation that can help you maintain the safety and efficiency of your operations.
By incorporating the REDEX® Flap into your pressure-relieved systems, you can have confidence that your equipment and personnel are protected against the potentially devastating consequences of explosion propagation. This investment in safety and reliability can pay dividends in the long run, ensuring the continued success of your operations and the well-being of your workforce.
As you navigate the challenges of maintaining the integrity of your pressure-relieved systems, the REDEX® Flap from RICO and CMC stands ready to be your trusted partner in explosion isolation. With its durable construction, low maintenance requirements, and advanced monitoring capabilities, the REDEX® Flap provides a reliable and versatile solution for safeguarding your critical industrial processes.
INTERESTED OR HAVE QUESTIONS? GET IN TOUCH WITH US NOW!