Celebrating 26 Years 1999-2025
Deflagration / Fast-Fire Protection Systems for Aerosol Gas Charging Room
The IEP high-rate discharge system provides deflagration and fast-fire protection for aerosol gas charging rooms, emphasising critical safety measures to reduce ignition risks associated with flammable propellants.
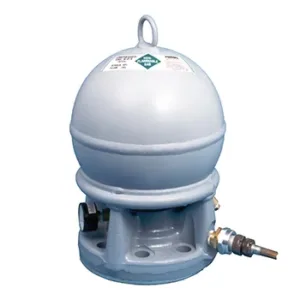
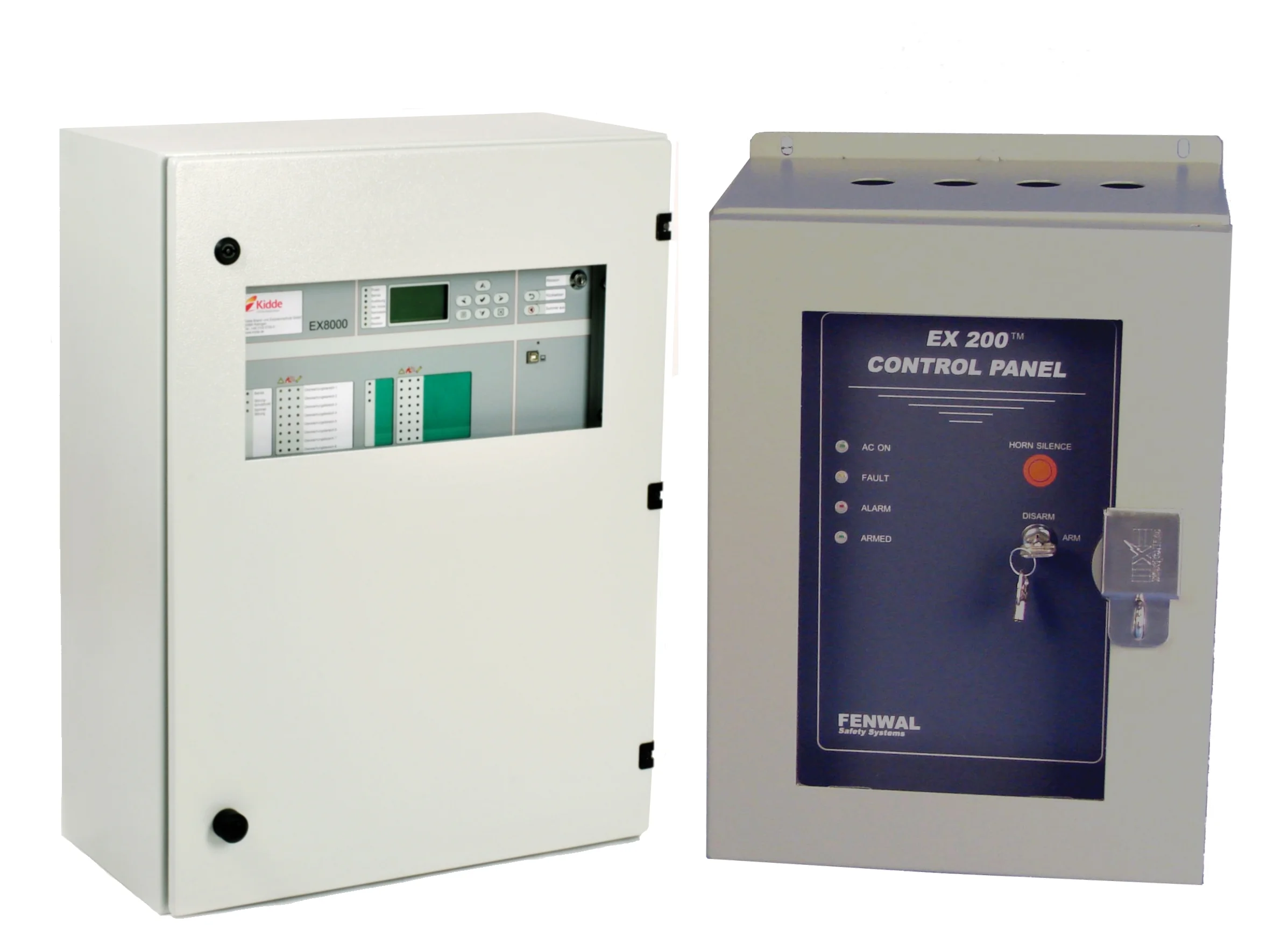
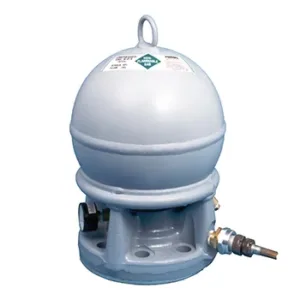
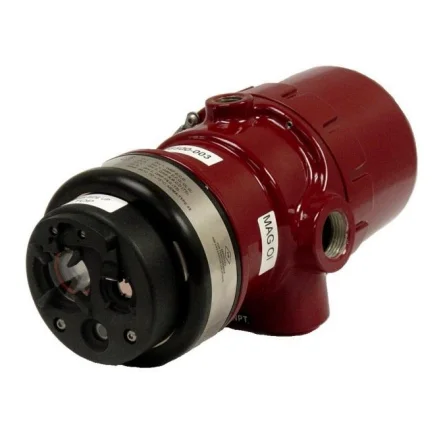
Application
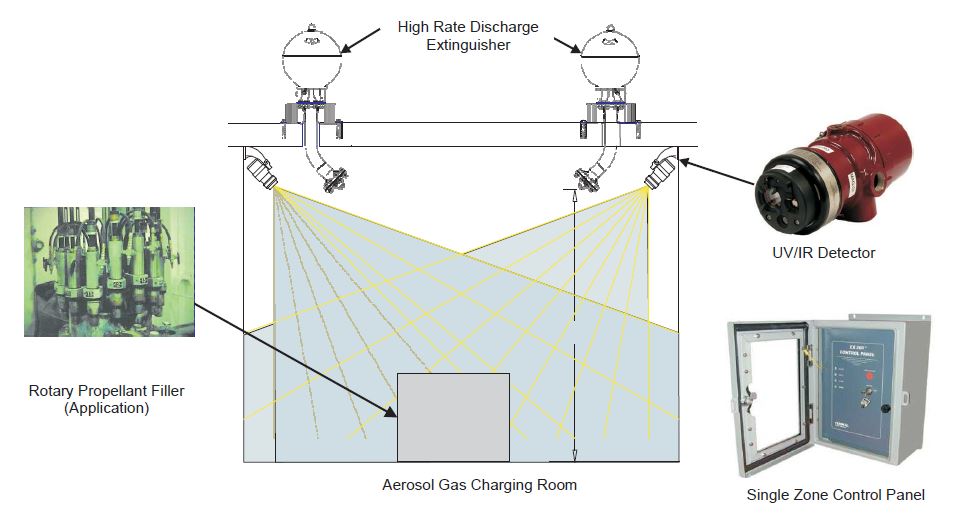
A typical aerosol packaging line is an automated system, incorporating conveyor systems and automated filling and charging systems. Aerosol cans are charged with various propellants. Most commonly these propellants are flammable hydrocarbons such as DME (dimethyl ether), Dymel® 152a, propane, butane, isobutane, or a blend of these hydrocarbon gases. These propellants are introduced into aerosol cans by high speed filling machines, some of which are capable of fill rates up to 450 cans per minute.
There are usually a number of personnel involved in the filling line operation to verify proper operation of the equipment, to remove damaged containers, and to provide maintenance or to shut down the line in case of a problem. Thus, the personnel may be present in the room while the risk of a deflagration exists within the gas charging room.
Major explosion risks in the aerosols industry occur during container filling and recovery, endangering worker safety. Small vapor leaks can trigger explosions if ignited. Protection relies on high-speed flame detection, explosion suppression systems (using rapid water discharge), prevention, ventilation, gas detection, and damage-limiting construction.
INTERESTED OR HAVE QUESTIONS? GET IN TOUCH WITH US NOW!
Hazard Analysis
Flammable propellants used in aerosol charging operations pose a risk of deflagration. While normal operations release small amounts of propellant, large air changes in the room design typically dilute this gas. However, equipment jams, charging line failures, material defects, or improperly sealed cans can lead to hazards. Local concentrations of flammable gas can create fireballs, threatening personnel. These gases require low-energy ignition sources, often triggered by static discharges or mechanical friction, allowing deflagration to occur before gas detectors can identify elevated levels.
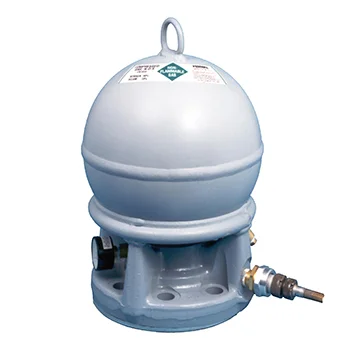
INTERESTED OR HAVE QUESTIONS? GET IN TOUCH WITH US NOW!
Protection System
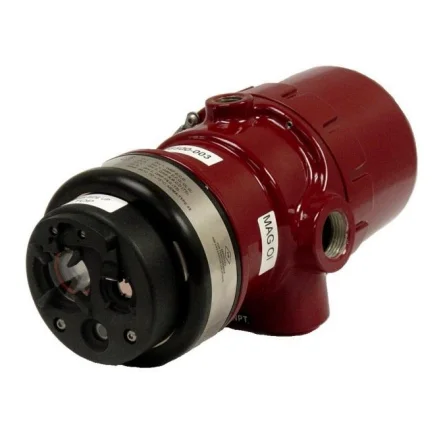
The aerosol gas charging room protection system meets the NFPA Standard No. 30B for deflagration suppression in aerosol filling facilities. It is designed to suppress localised deflagrations from hydrocarbon propellant gases using high-rate discharge (HRD) suppressors filled with distilled water. These suppressors are installed indoors at temperatures above freezing.
Ultraviolet/infrared (UV/IR) sensors detect deflagrations and send signals to the control panel, which triggers the HRD suppressors to discharge suppressant. The control panel also shuts down conveyor drives, gas solenoids, and hydrocarbon pumps to prevent fire spread and reduce re-ignition risks. Exhaust fans operate at maximum speed to remove any remaining vapours from the room.
INTERESTED OR HAVE QUESTIONS? GET IN TOUCH WITH US NOW!
UV/IR Flame Detector Specification Details
- Detects both UV and IR radiation for high false alarm immunity.
- Automatic Optical Integrity (AOI) self-checks optical and circuit health.
- Fast, reliable detection with visual status via tri-color LED.
- Immune to false alarms from lightning, sunlight, hot objects, or non-UV lights.
- CE marked, ATEX compliant.
- Used with IEP Technologies control units to quickly detect flames and activate explosion protection in areas with gas or vapor hazards.
- Housed in an explosion-proof aluminium enclosure; includes internal self-testing of sensors and optics.
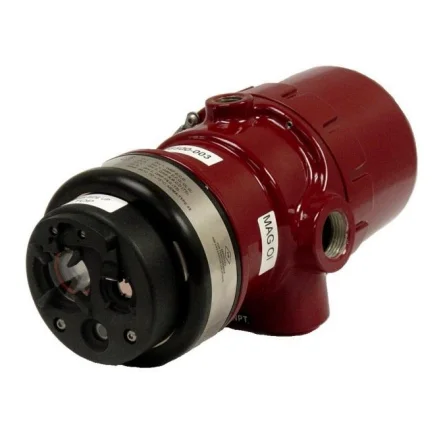
WANT MORE TECHNICAL DETAILS? DOWNLOAD OUR DATASHEET.
INTERESTED OR HAVE QUESTIONS? GET IN TOUCH WITH US NOW!